Quality
Introduction
Quality plays an important role either in manufacturing or service industries. Controlling and improving quality has become an important strategy in both industries. In this competitive world, quality has become one of the most important customer decision factors in the selection of various products and services. Thus for a profitable business, an organisation should impress customers by providing good quality products or services.
For example, we use products or services every now and then. Let say, it doesn’t meet our expectation which means it is of bad quality. And ‘if it satisfies our requirement then it is of good quality’. We should keep in mind that, regardless of the grade, the quality should be good. In any case, the quality cannot be compromised. Thus quality is a value for a performance or a service.
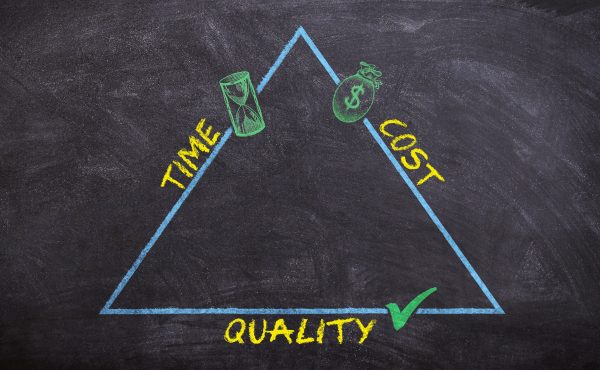
Definition of Quality
Quality can be generally defined as a “fitness for intended use”. It can be defined on a various ways w.r.t manufacturing, service processes and so forth. Let’s discuss some of them.
- Manufacturing – To manufacture products w.r.t quality of conformance. So it meets the expectations of a customer by manufacturing defects free products.
- Service – To provide excellent services without any interventions and to meet customer expectations. Thus able to achieve higher customer satisfaction.
Whether in discrete, process manufacturing and service industry – achieving customer satisfaction is the highest level of quality. So apply techniques which can help to gain detailed insights into customer requirements and ability to provide services or products to meet or exceed their expectations. Hence it is important to understand the Voice of the Customer.
There were many phases in the evolution of quality. Several genius minds have been instrumental to developed the concepts of quality which are known today. Let’s have a brief overview of the evolution of quality.
During the 1920s, Walter A. Shewhart introduced statistical process control (SPC) to control and monitor variation in a process by the usage of ‘Control chart’. His work was later forwarded by W. Edwards Deming. He successfully applied Shewhart’s methods during World War II to improve quality in the manufacture of weapons. After the war had ended, Deming and Joseph M. Juran introduced SPC & quality management methods to Japanese industry. It was implemented successful for quality improvement goals. Later it was widely known as Total Quality Management (TQM).
In 1980s, Total Quality Management gained a lot of popularity outside Japan. Various methods were introduced to support TQM. These includes Lean manufacturing and six – sigma. Several quality initiatives were followed – BS, EFQM, ISO 9000, AIAG, etc. During the initial phase, quality was applicable only on manufacturing sector but now it has moved into areas like healthcare, financial institutions, academic, airlines and so forth.
It was introduced by Kaoru Ishikawa (renowned Japanese Professor). He pioneered quality control activities in Japan. With the usage of these basic tools, 95% of the variation could be eliminated from a process.
- Check sheet – It is a form of the document for organizing and collecting data in real time process or in a location where the data is generated. It helps us to understand the process & to keep track of defect patterns including the causes.
- Pareto chart – It is a special type of chart which combines both bar graph and a line graph to represent the factors which are affecting the variable. Highlights the most frequently occurring defects & used to determine priorities for quality improvement.
- Histogram – It is a pictorial representation which displays the data value in bars. It gives an easy understanding of a process line.
- Scatterplot – It is a simple graph where the data of two continuous variables are plotted against each other. It helps to identify the strength of the relationship between two factors & their cause and effect relationship.
- Cause and effect diagram – Also popularly known as Fishbone diagram. It is a tool to explore the causes and to display as many as possible causes that might be creating a problem.
- Control Chart – It is a graph which displays all the process data in order sequence and detects variation in a process. It prevents us from manufacturing defective product.
- Stratification – It is a method to divide the data into categories or groups (homogeneous kind). It helps to identify the source of variation from which categories of data and reduction in sampling error.
In our daily life, we utilize a variety of products such as mobile, electrical bulbs, clothes, etc. All these products should attain a certain quality level when we use it, whether it can be good or bad. We are in a tough competitive world and so the main aim of a company is to produce good quality products. Thus, able to increase productivity, profitability and achieve customer satisfaction.
Let’s discuss some of the possibilities, “Why the company is producing bad quality products?”
- Quality by design – To improve quality, products should be well designed with reference to customer, market and robustness.
- Quality of conformance – It is the ability of a product to meet design specifications. Therefore, the finished products should conform to the design specifications.
- Improper training – Proper training should be given to all the employees about “How to achieve quality?” With proper educational knowledge, they could achieve quality improvement goals.
- Lack of Commitment – Quality is a long term commitment. So there should always continuous improvement even after achieving a certain quality level.
Quality plays a significant role in organization growth and performance. It is a crucial parameter which differentiates an organization from its competitors. An organization should implement a set of procedures to ensure that the products or service meet the quality standards.
- To meet customer expectations – Quality plays a crucial role for greater customer satisfaction. In this competitive market, an organization should produce good quality products or else customers would choose the best one from the availability. Thus losing the markets and reputation.
- To increase profitability – It increases profitability. When a good quality services are provided to a customers, they would enhance loyalty and thus increases profits to an organization.
- To meet a good reputation – By the word “Quality”, it reflects an organization’s image and achieves a good reputation in the customer’s eye. Poor quality of products or services leads to a negative aspect and thus hamper the company’s image.
- Managing costs – By producing good quality products, we could reduce costs and enhance efficiency. Poor quality costs a company in terms of productivity and thus increases costs.
- To meet industry standards – “If an organization produces good quality products then only they would be able to meet certain industrial standards like ISO, AIAG, BIS, etc.”
Quality is the most significant factor in determining the long run success of the organizations. Focusing on quality helps keep a company strong in all areas. To achieve quality, organizations could implement big methods like TQM principles, Lean manufacturing, Six Sigma, and Lean Six Sigma. But sometimes we could not able to implement such methods – due to time constraints, complications, costs, organization size, oriented issues, etc.
Some common techniques used to support Quality are –
- Measurement system analysis (MSA) – MSA is a method to determine whether the measurement system is acceptable or not. It helps us to find variation due to measurement system and guide us to improve the system for measurement.
- Design of Experiment (DOE) – DOE is a method used for new product design and formulation, manufacturing process development and process improvement. It provides a cost-effective method to understand and optimize products and processes.
- Statistical process control (SPC) – SPC is a method used to monitor, control and improve processes by eliminating variation. It is widely used in almost all manufacturing processes and service industry for achieving process stability to continuous improvements in product & service quality.
Quality is important in every aspect of our lives. When we buy gadgets it must meet our expectations by giving better performance, durability and features. Similarly, when we buy ingredients for foods, it must meet certain standards like quantity, taste, packaging and so forth.
In industrial sectors (either in manufacturing or service), it plays a major role in maintaining the standards of an organization. Controlling and improving quality has become an important strategy in both industries. In this competitive world, quality has become one of the most important customer decision factors in the selection of various products and services.
There are certain quality standards which are compulsory for the industry to attain and thus ensure customers to use it without a doubt. When we buy a product and it doesn’t meet our expectations like features, performance, serviceability, reliability, etc. – then “Will we buy a particular product again?” Just think about it. Thus for a profitable business, an organization should impress customers by providing good quality products or services.
Some popularly used industrial quality standards
- ISO – It stands for International Organization for Standardization. ISO is globally recognized for its standards whether it can be automotive, medical devices, services, IT and so forth. It was founded in February 1947 in the United Kingdom and it’s headquartered is in Geneva, Switzerland. It is an independent, non-governmental international organization with a membership of 164 national standards bodies. It periodically updates and releases guidelines for quality management systems.
ISO 9001 is commonly used certification for quality. It contains seven key principles of quality management –
Customer orientation
Leadership
Engagement of people
Process approach
Continuous Improvement
Evidence based – decision making
Relationship management
- BIS – It stands for Bureau of Indian Standards. It was established in December 1986 and it’s headquartered is in New Delhi. We can recognize BIS certified products or services by ISI mark and Hallmark. It is a member of ISO. Its core activities of standardization and conformity assessment has been benefiting the national economy by providing safe, reliable and quality goods, minimizing health hazards to consumers, protecting the environment and much more. It started the scheme with Quality Management System Certification (IS/ISO 9001) and over the years it has gradually expanded its activities to various other Management Systems also (IS/ISO 14001, IS 18001, etc.).
It involves in various activities –
- Standards formulation
- Product certification scheme
- Foreign Manufacturers Certification scheme
- Hallmarking scheme
Attend our Training Program, to know – “How can we achieve Quality Excellence in an Organisation?” We conduct various training programs – Statistical Training and Minitab Software Training. Some of the Statistical training certified courses are Predictive Analytics Masterclass, Essential Statistics For Business Analytics, SPC Masterclass, DOE Masterclass, etc. (Basic to Advanced Level). Some of the Minitab software training certified courses are Minitab Essentials, Statistical Tools for Pharmaceuticals, Statistical Quality Analysis & Factorial Designs, etc. (Basic to Advanced Level).
We also provide wide-ranging solutions for Enterprise Quality Management to achieve Organisational Excellence.